How to Choose the Right Vibrating Screener for Your Mining Operation
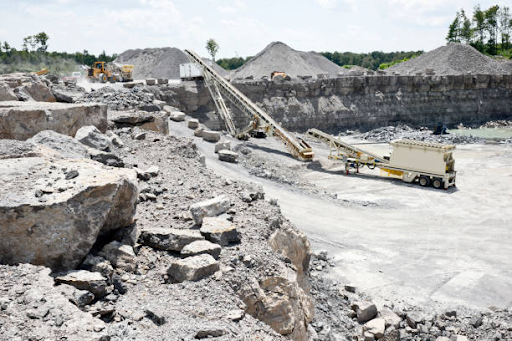
The rising need for effective material handling and separation in the mining sector help improve productivity while reducing operational costs requires mining professionals to consider new advanced techniques. Magnetic separator conveyor belt screening systems are records in active development and the best usage for industry paired with vibrating separators. This article aims to discuss the important aspects of selecting a vibrating screener that guarantees proper functionality and results in cost saving to the client while mining in the field.
The Importance of Vibrating Screeners in Mining Operations
Screener separators are used to sort materials with regard to their dimensions and size by means of producing vibrations through driven motors or imbalanced rotor weights. These machines are necessary to the mining industry so that ores, aggregates and the like shall be segregated. Only particles of the right dimensions shall be advanced in the production line while the oversized and the undersized materials shall be discarded or processed differently. Moreover, effective vibrating screeners not only assist in the separation process but also positively affect productivity for the machines, putting a cap on the unwanted standstill time caused by blockage. Furthermore, these machines have enhanced efficiency as they decrease the material handling problems which disrupt the working process and thus, are greatly enjoyed by the world of mining.
The combination of the vibrating screeners and the magnetic separator conveyor belts allows for efficient elimination of ferrous contaminants from the materials during the processes. This combination is particularly useful in mining operations where purity and precision are critical. The combination of these two external devices—and the processes of screening and conveying—yields tangible results in the reduction of nonproductive operations, improvement of material quality, and smooth running of the production processes.
Key Factors to Consider When Selecting a Vibrating Screener
Selection of a vibrating screener for your mining operation should be carried out systematically in order to achieve the most productive results. First, consider the type of material you are separating, because it will control the screen division, vibration frequency, vibration amplitude, and, consequently, the quality of separation. Materials of different moisture and/or particle size distributions may need certain shapes screens to work properly, such as circular or linear screeners. Another concern worth addressing is the abrasiveness of the material; more abrasive materials wear down equipment and thus may require equipment designed to withstand such conditions.
Side sifting screens can also be used to replace conventional screens. When using sifting screens, one should always measure the throughput capacity as it is crucial. Such screens made of sturdy materials will undoubtedly have a longer lifespan. This is particularly true since they will be receiving much more wear and tear than conventional screens. It would also be prudent to use them with a magnetic separator conveyor belt. These features will boost the separation efficiency as well as lowering the amount of contamination and other materials that can be removed. Forward looking thinking is also important as future scalability can be achieved easily by using a form of versatile screens.
Models of Vibrating Screeners For Mining Use
There is a huge variety of vibrating screeners for mining, each with varying functions. Linear vibrating screeners can be used effectively for the classification of dry materials such as crushed stone, sand and ores. Using these types of screening machines, it is possible to separate coarse and fine materials with linear motion. These machines are widely applied in mining where accurate classification of material into grades is required. With circular vibrating screeners, materials that have high moisture content can efficiently be screened as their circular motion prevents clogging and improves throughput. These machines are particularly useful for ensuring that wet materials or materials that tend to stick to the screening surface do not interfere with the productivity of the screen. Finally, multi deck vibrating screeners are used to make separation of different sizes of materials into several functions simultaneously in one pass for precise classifications.
Once separation requirements and properties of the material are clear, you will know what type of screener to consider for your mining operation. For those who are concerned with contamination control, these screeners can be mounted on conveyor belts that have magnetic separators integrated into them to increase the purity of material outputs. This integration is important for mining clean up efforts as well as operational efficiency.
Benefits of Combining Vibrating Screeners with Magnetic Separator Conveyor Belts
The integration of vibrating screeners with magnetic separator conveyor belts is extremely beneficial for mining operations. Even complicated material separation can be automated with little to no waste or contamination. The value of technique stems from the reliance on magnetic separator conveyor belts to handle the separation of ferrous materials from non-magnetic substances which is one often challenging for humans to carry out. For mining operations where profitability directly correlates to effective resource recovery, this combination is key.
This integration also reduces instances of equipment failure that stems from contaminants. With a combined use of vibrating screeners and magnetic separators, technology tailored to removing ineffective particles that tamper outputs, cleaner outputs and improved overall efficiency can be achieved. Equally, this combination reduces the required investment in labor, directly reducing costs such as wages. For all businesses globally, the ability for equipment to achieve better and consistent end-products translates into business growth as maintenance and equipment failure downtime is drastically reduced. For mining operations aiming for high-quality results, this combination is a breakthrough in technology.
Conclusion
In choosing a vibrating screener for your mining operation, consideration of screen material, throughput, and its compatibility with other equipment is crucial. The combination of vibrating screens and magnetic separator conveyor belts can achieve an exceptionally high level of precision and efficiency in the processing of materials. The optimization of mining practices, cost reduction, and improvement of resource recovery can be achieved through proper selection and maintenance of equipment.
The integration of a screener with a magnetic separator conveyor belt allows for greater material quality, less waste, and greater efficiency. This means that in investing in the correct mining equipment tailored to your specific needs, easier and better streamlined processes can be achieved in the industry. It does not matter if you are dealing with fine materials or bulk loads; the right screener is sure to improve productivity and level of success drastically.